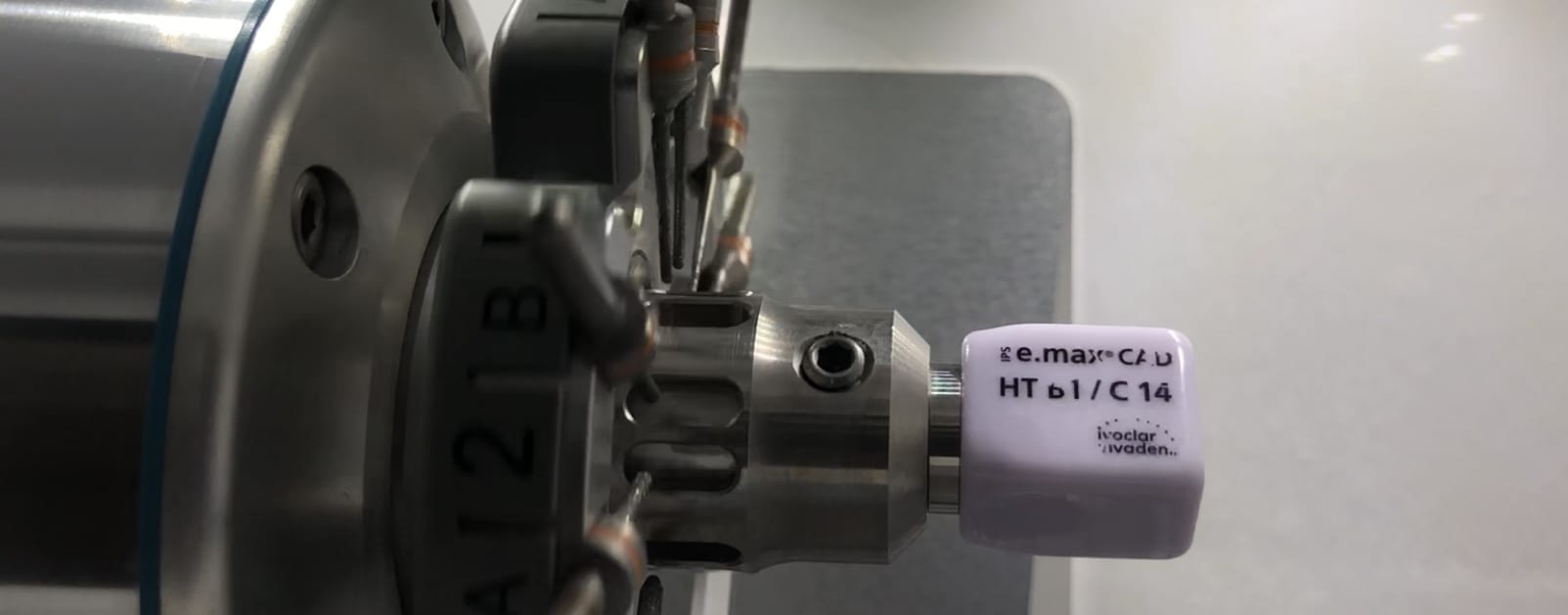
This a very common question we get at CAD-Ray.com and it reflects on how little dentists understand about digital impressions and CAD/CAM in general.
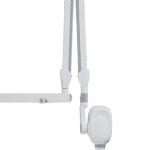
It reminds me of a dental conference I want to, fresh out of school, placing orders for our start-up practice. As we went to the X-Ray equipment section, one of the first things the representative said to us was that their machines are “Digital Ready”! We all had good laugh explaining to the rep that the machine had nothing to do with digital X-Rays, the sensors did!
We feel the same way with digital impressions and CAD/CAM platforms when people talk about integration and making sure one “product talks to the another ” and how it all needs to be developed by the same single manufacturer. It’s loaded with a lot of inaccuracies and misrepresentations.
The reality is that every system has its flaws and can have just as much trouble talking to a machine manufactured by the same company! As dentists, we are much smarter with our decision processes now, but it is still a buyer-be-ware landscape.
Here are some basics you should appreciate before committing to a high ticket item. It’s imperative to understand that imaging has little to no impact on milling. These are completely independent processes- let us explain:
You can image (take an intra-oral scan) with system A. Then you can take the data from system A and take it to CAD software of system B. A lot can go wrong here at this step alone. Simple examples include;
- The patient name doesn’t come along with the data.
- Incorrect data may come across with incorrect information- you can have the occlusal relationship look perfect in system A but when it goes to CAD, the bite can be off.
- You mark your margins in A, but they are distorted in cad software. So you have to make sure this works.
Keep in mind that this can even happen if you stay within a “System A” or “complete system”. Luckily a lot of this is ironed out already with legacy and legitimate products and competent practitioners. Now comes the design step. You have a few choices; exocad and 3shape being the leaders. If exocad does the margin placement and the final restoration from start to finish, a lot of errors are eliminated.
After the design process, comes the nesting and manufacturing. At this step, the milling machine has NO idea what iOS you have used. It’s just data for a restoration that it needs to process. Ar this most vulnerable step, we need to make sure the CAM software for a particular machine can interpret the design software that did the nesting. A lot happens here;
[videopress yOHyMMVp permalink=”false” hd=”true” loop=”true” autoplay=”true”]- How’s the restoration positioned in block?
- What size block / puck?
- What materials? What speed? What detail?
- What are sizes of burs in mill, etc…
Then comes the consideration for your milling needs.
- You can mill soft ceramics for 15,000$
- For a little more, you can wet mill emax
- Cross the 30k barrier with and you can cut zirconia (we do NOT recommend in office zirconia- dumbest thing you can do)
- Closer to 40k and you can do in house metal custom abutments.
- Over 40k you can mill roundhouse bridges and you are as much a labtech as a dentist.
The trickiest part of all this is the last step. Making sure the mill has the right cam to talk to design software. This can be a nightmare if you don’t do your homework.
So, with the Medit iOS you can mill to any machine. You can even take it to cerec inlab software and Jump through a lot of hoops to mill with CEREC chair side milling machine. Not worth the headache!
The CEREC chairside mill remains the fastest carver of emax restorations, but it can come at a cost – you need to bulk out the margins so they don’t break off at mill.
You must log in to post a comment.